How Are SIPs Made?
Structural insulated panels (SIPs) are made by bonding an insulating foam core between two engineered wood or fiber cement boards. Visually, SIPs are said to resemble an ice cream sandwich, with the insulation forming the core and the boards creating a rigid, protective shell. Manufacturers typically begin with the insulating core, which can vary from expanded polystyrene (EPS) to more energy-efficient options like high-performance graphite polystyrene (GPS). From there, the outer layers may consist of oriented strand board (OSB), plywood, gypsum, or fiber cement, depending on the project’s needs. Once bonded with structural-grade adhesives and compressed, SIPs become durable, airtight panels that can be custom-cut to any shape or size.
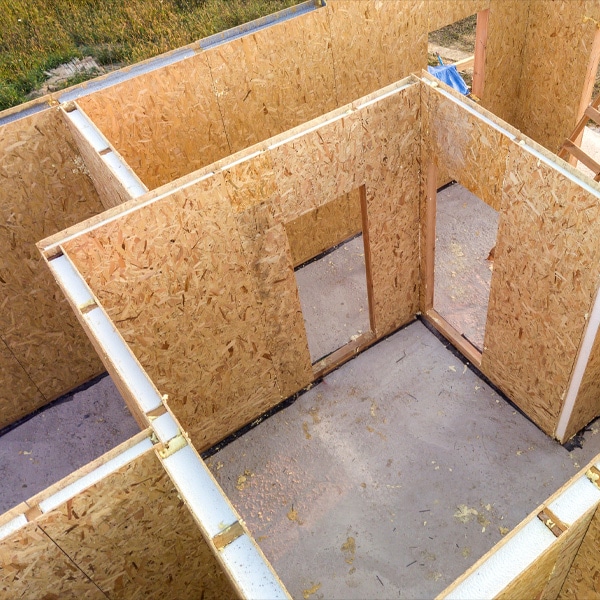
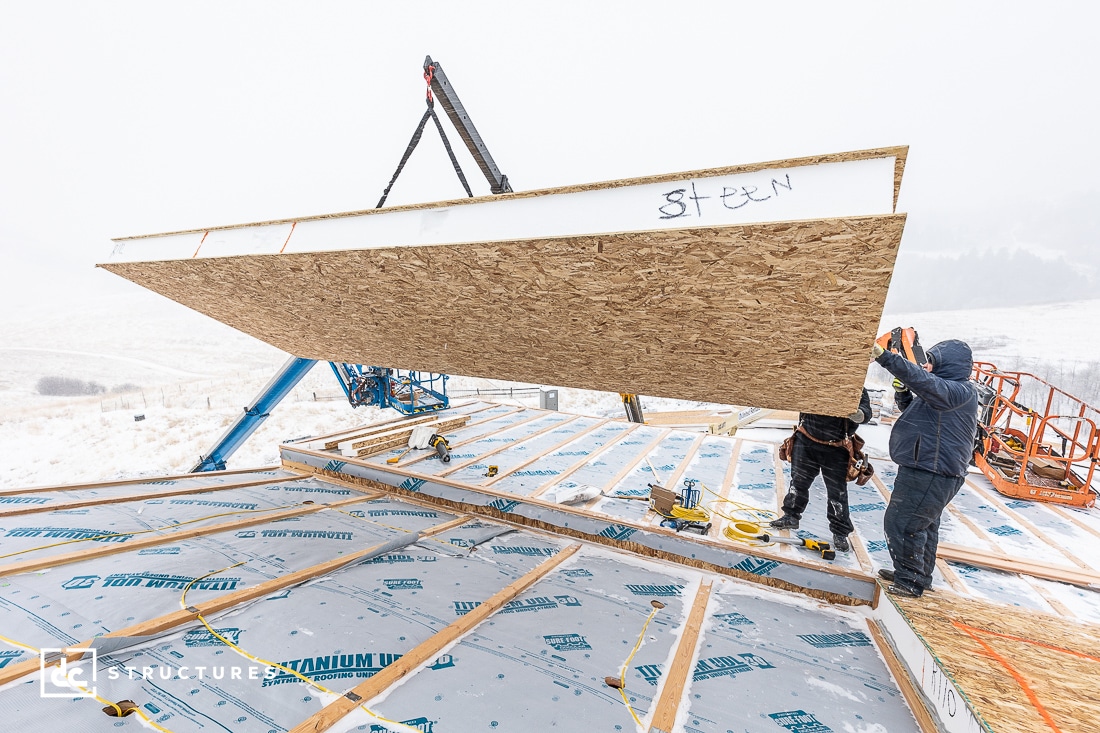
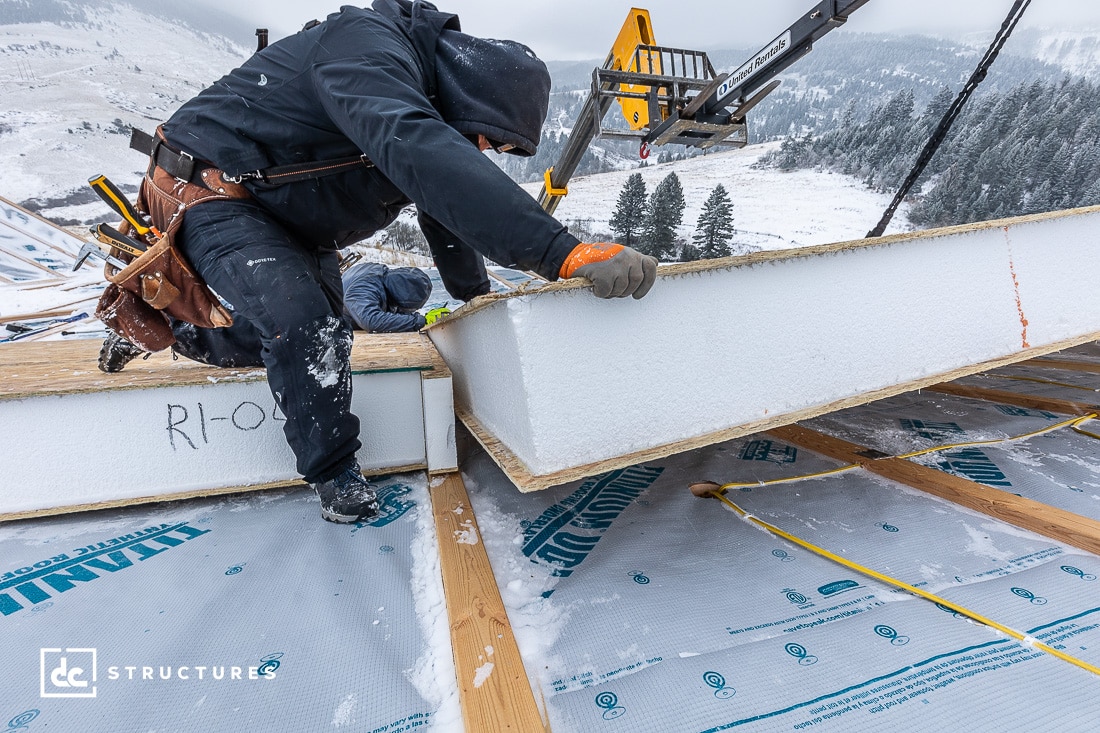
Where Are They Used?
SIPs are widely used in residential, commercial, and industrial buildings, including single-family homes, retail spaces, schools, and warehouses. Their exceptional energy efficiency makes them particularly popular in regions with strict building codes, where high insulation and airtightness standards need to be met.
Because SIPs have lower embodied carbon than alternatives like steel, concrete, and masonry, they are an ideal choice for projects requiring high R-values—delivering superior insulation and reduced energy consumption. Their airtight construction also provides optimal thermal performance, making SIPs a smart, sustainable solution for colder climates and energy-conscious builds.